パナソニックグループの新体制に伴い、100年にわたる歴史を持つ電池事業を引き継ぎ発足した事業会社。“未来を変えるエナジーになる”をビジョンに掲げ、乾電池をはじめ産業用電池や車載用電池といったBtoB事業をグローバルに展開している

要素開発5部 開発1課
九州大学大学院総合理工学府卒業。在学中はナノ材料化学研究室に在籍し、無機金属酸化物ナノワイヤについて研究。2019年、パナソニック(現・パナソニック エナジー)エナジーテクノロジーセンターに入社。以来、リチウムイオン電池の次世代極板製造プロセスにおける要素技術開発業務に従事
時間をかけてあらゆる可能性を仮説検証したその先に
化学の英知を結集した最先端電池を世界に届けられる
家族のために料理をするのが好きだった幼少時代。料理は化学反応でできている。そう気づいた頃には、白衣を着て研究している自分の姿を思い描いていました。高校では化学科に進学し、大学院では無機材料を研究。そのまま博士課程へ進む道もありましたが、研究室でのパナソニックとの共同研究を通して、コスト・人員・スピード、全てが大学とは桁違いである規模の大きさに引かれ、企業への就職を決意しました。また、自分の手掛けた製品をエンドユーザーに届けたい気持ちもありました。電池はまさに化学反応を利用したデバイスです。世界トップクラスの技術力を誇る当社で、ものづくりに挑戦したい。そう考えて入社を決めたのです。
大学院での研究内容から配属先は材料開発を想像していましたが、入社後はプロセス開発部門に配属されました。材料開発が材料を一から作り出していく作業であるのに対し、プロセス開発は完成した材料を使ってどう製品開発につなげるかの作業。ものづくりには一歩近づくとはいえ、業務領域が大きく異なるため、当初は聞き慣れない専門用語や手法の違いに戸惑うことも多くありました。それでも、3年目くらいにはひと通り把握でき、徐々にモチベーションも向上。「どうやって良い材料を作るか」に意識が向いていたそれまでと違い、「いかに材料を使いこなして開発を進めるか」に面白みを見いだせるようになりました。これは、企業の研究職に就いたから、そして当社ならではの研究基盤があるからこそ、得られた気づきだと思っています。現在は、電気自動車向けリチウムイオン電池の開発に従事。具体的には、リチウムイオン電池内にある「電池極板」の製造プロセスに関する技術開発を行っており、次世代極板の生産実現に向けて日々奮闘しています。
サンプルの性能評価技術を開拓
次世代極板の製造に希望が見えた
電池極板の製造プロセスには、いくつか工程があります。材料を混ぜ合わせて塗料化する工程、塗料を極板の土台に塗る工程、塗料を乾燥させる工程、極板をプレスしてロール状にする工程などです。従来のプロセスでは、乾燥工程で多量のCO2が排出されるという課題がありました。業界全体に環境配慮が求められる中、私のミッションは、乾燥工程が不要なドライ塗工技術を確立すること。中でも私は、極板の性能を大きく左右する塗料化工程を担当しています。ドライ塗工に携わって約4年、最も印象に残っているのは、極板サンプルの性能評価技術を開拓したことです。当社では極板の製造手法が10年以上変わっておらず、ドライ塗工はまさに手探りの状態でスタートしました。一つ一つ手作りしたサンプルを性能評価するにも、明確な指標がないため担当者によって出来栄えにむらがあることが課題でした。そこで私は、社内外の有識者や解析機関と連携し、評価基準とすべきデータの数値化や可視化に成功。その結果、開発スピードが劇的に改善し、サンプルの量産化にも希望が見えました。当初は5名ほどのチームでしたが、研究が進むにつれて社内の注目度も高まり、現在は20名を超える規模に成長。今後の量産化次第では、さらに大きなプロジェクトになる見込みです。
研究開発は、すぐに結果が出るものではありません。それでも、目の前の小さな目標を一つずつクリアするごとに達成感があります。そして、自分の作った製品が世の中に供給される。それこそが、ものづくりの醍醐味です。化学の研究者になりたい。仕事選びにおいて私は、揺るぎない軸がありました。もしも今、挑戦したい仕事があって、自分が働いている姿をイメージできたなら、それが天職だと思います。
工場での現場実習と海外視察 製品開発への意欲が高まる
入社後、電池工場のラインでの1カ月間の実習と、海外電池工場の視察を経験。製造工程に加えて、現場で働く方たちにお会いしたことで、「この人たちが作りたいと思えるような電池を開発したい」と強く思いました
次世代極板の技術開発に参加 チームプレーの重要性を学ぶ
2年目で新規極板製造プロセスの開発プロジェクトに参画し、一つの目標に向かってチームで動く大切さを学びました。材料メーカーや商社など、社外の方との接点も増え、社会人としての基礎も身に付いたと実感しています
ドライ塗工による試作品が完成 量産化に向けて大きく前進
手作業で1000枚以上もの極板の試作を繰り返し、ようやく納得できるレベルに到達。量産化に向けて、大きく前進しました。このときの成功体験が、現行の極板開発に取り組むモチベーションにつながっています
課題設定の研修を通して 研究の社会的意義を再認識
昇格研修を受ける中で、自ら課題設定を行うプログラムがありました。自分の仕事がなぜ存在し、世の中にどんなインパクトを与えるのか。深く考え抜いたこのときの経験は、私にとって大きな財産になっています
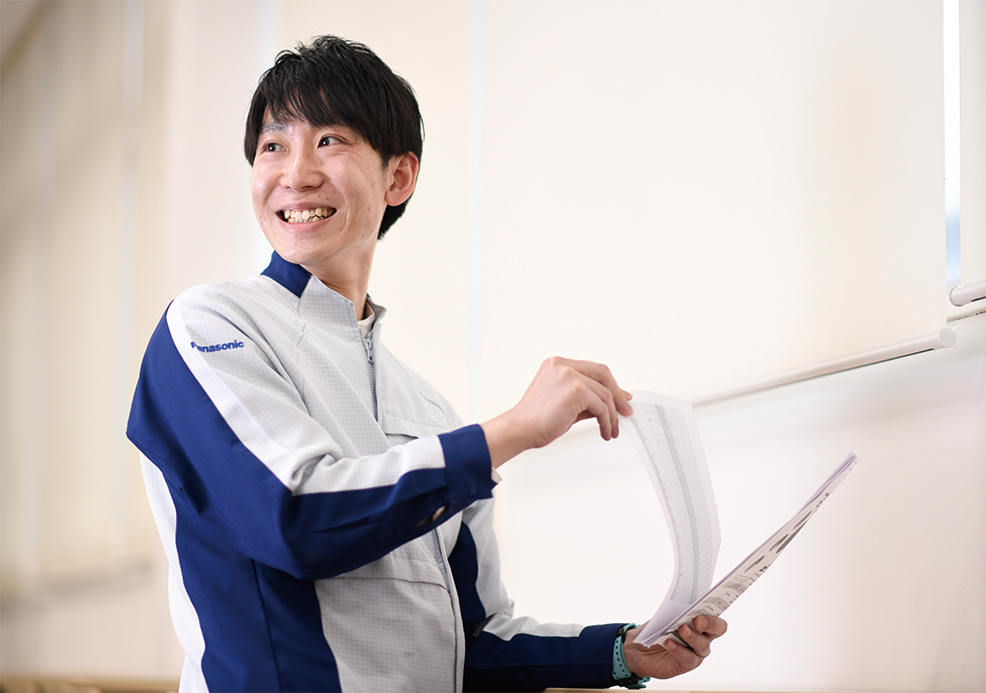